产品中心 XINPENG PRODUCTS
业务范围 CUSTOMIZATION
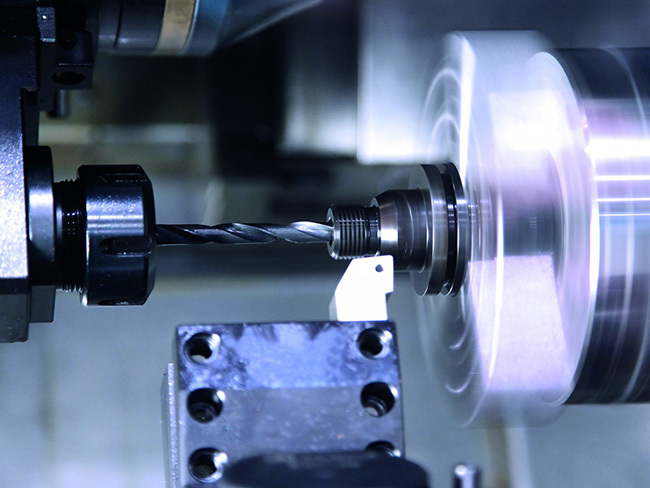

CNC加工
自动车床加工
数控车床加工
铣床磨床加工
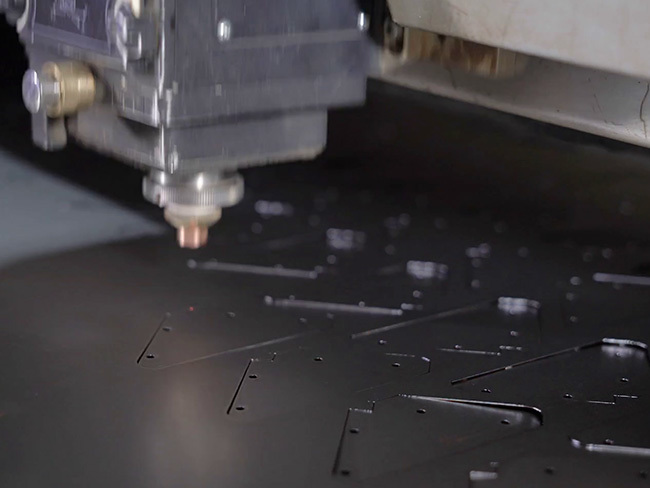

铝合金产品研发定制
精密零件配件加工
3C数码外壳类加工
工装夹具治具定制加工
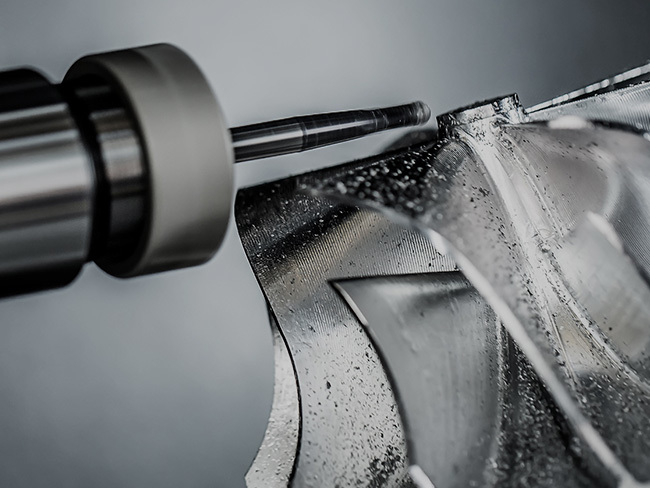

不锈钢、铁件加工
铜铝件加工
绝缘体材料加工
氧化、电镀等后处理加工
新闻中心 NEWS CENTER
TEL
0317-4220938(座机)
15033362732(手机)
FAX
0317-4315396(传真)
info@china-xp.cn(邮箱)
ADD
中国•河北•青县 青县耿官屯工业开发区
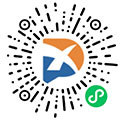
微信小程序